- Room 1807, Unit 9, Building 2, Shangxing Commercial Street, Shangde Road, Shangxing Community, Xinqiao Subdistrict, Bao'an District, Shenzhen City, China
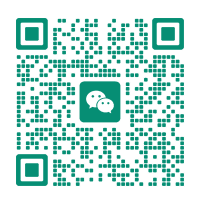
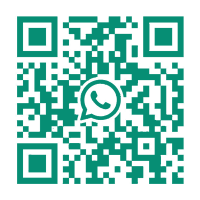
Aerospace & UAV
WJ Prototypes is your 3D manufacturing partner from prototype to large scale production.
Consumer Electronics
New Product Introduction Solutions for Consumer Electronics.
Robotics & Automation
Need some assistance bringing your robotic device or parts from the sketch-board to reality?
Medical Devices
The medical industry needs high quality, dependable and safe parts and products.
Automotive
New Product Introduction Solutions for Automotive
Industrial Machinery
The main purpose of industrial prototyping is to take the product from drawings into the real world.
Have you ever considered the reasons behind defects such as cracks or surface imperfections in your brass components? Do you find it challenging to maintain consistent quality across various production batches? These are prevalent issues encountered by many manufacturers in the realm of brass metal casting. Whether your focus is on plumbing fixtures, electrical components, or decorative items, achieving superior quality in brass metal castings is vital for the success of your projects. So, what makes this process so complex? Let us explore the intricacies of brass metal casting to identify the underlying challenges and uncover effective solutions.
Brass is an alloy of copper (Cu) and zinc (Zn), typically about 60–70% Cu and 30–40% Zn. Small amounts of other elements (lead, tin, aluminum, etc.) are added to tailor properties – for example, lead improves machinability. These alloying choices give brass its distinctive traits: it forms a protective oxide layer (so it doesn’t rust) and is highly malleable, making it ideal for intricate castings. Brass also conducts heat and electricity well.
By mastering these properties, we know how brass will behave during casting and how to adjust our process.
A well-designed mold (with gates, runners and vents) is essential so molten brass flows evenly and air can escape. At WJ Prototypes, we begin by melting the brass alloy to about 900–940 °C (1650–1720 °F). Precise temperature control is critical: if the metal is too cool, it won’t fill thin sections; if it’s too hot, brass can oxidize or burn, creating defects. We use controlled melting furnaces and thermal sensors to hit the sweet spot for flow without degradation.
Our Casting Services:
1. Vacuum Casting
2. Die Casting
3. Rapid Injection Molding
We pour the molten brass into the mold at a carefully controlled rate. Pouring too fast can trap air and cause porosity, while pouring too slow can let the metal solidify prematurely. That’s why our engineers design the gating system (sprue, runner, gates, and vents) to allow smooth flow and air escape. For example, adding vents or vacuum-degassing can draw out gases before filling.
For low-volume or prototyping jobs, we often use green-sand or phenolic sand molds (which are cost-effective and easily changed). For higher-volume precision work, we use metal or ceramic permanent molds that capture fine detail. Regardless of the mold type, we ensure adequate risers and chillers are placed. Risers are extra metal reservoirs that feed the casting as it cools, so shrinkage happens there, not in the part. Finite-element pouring simulations (and past experience) guide our mold layout to avoid cold shuts or misruns.
You can submit your designs to us through our contact us page
OR Email to info@wjprototypes.com
Even with good design, common casting defects can occur. The most frequent issues in brass castings are gas porosity, shrinkage cavities, and non-metallic inclusions. WJ Prototypes implements targeted solutions to eliminate these problems:
By engineering the process this way, we tackle defects at the source. In bullet summary: vent and vacuum to reduce trapped gas; add risers and chills to feed shrinkage; and filter/clean the melt to avoid inclusions.
After casting and rough cool-down, each brass part is machined to final dimensions with tight precision. Our CNC milling and turning centers routinely achieve tolerances around ±0.001 inches (±0.020 mm), which is crucial for components used in aerospace or automotive assemblies. Once the metal is in shape, we deburr, polish, or plate (nickel, chrome, etc.) the surface to meet appearance and corrosion-resistance requirements. For decorative or antique-style parts, we can also apply a chemical patina for a custom finish.
We enforce strict quality control at every stage. Non-destructive tests (such as X-ray or ultrasonic inspection) scan for any hidden voids or cracks inside the part. We pair this with Statistical Process Control (SPC): key data like melt temperature and pour rate are logged during production, and automated systems flag any drift beyond our control limits. This way, if we see a trend toward deviation, we correct it immediately – preventing an entire batch of bad parts.
CNC tools refine each casting to spec. For example, shafts or threads cut into the brass are finished to within 0.01 mm, ensuring assemblies fit and function perfectly.
Parts are polished smooth and coated as needed. Standard finishes include nickel or chrome plating for corrosion and aesthetics; alternatively, we apply colored chemical patinas for a handcrafted look.
X-ray/ultrasonic tests check for internal porosity or cracks. All dimensions are verified with coordinate measuring machines (CMMs) and visual checks. SPC software tracks production parameters continuously, so our output stays consistent from prototype through volume production.
At WJ Prototypes, we bridge the gap between one-off prototypes and large-scale runs. Thanks to our huge China facility (12,000 m² with 150+ engineers and 200+ machines), we cover the full spectrum of manufacturing services in-house. This end-to-end capability means you get expert design-for-manufacture support right from the start, and a seamless handoff to production later. Key benefits include:
By leveraging our China footprint, we help clients launch products cost-effectively at any scale. The combination of agile prototyping and deep-volume production is a strategic advantage: early-stage issues are resolved before committing to tooling, and then large batches flow without redesign overhead.
Brass casting in China truly blends artistry with scientific expertise: it takes material knowledge, precise process control, and careful craftsmanship to turn molten brass into a perfect finished part. At WJ Prototypes, we’ve built that bridge. We use advanced tools and techniques (from 3D CAD simulation to vacuum furnaces and SPC) so that common issues like porosity or shrinkage never stand in the way of quality. Combined with our global network, this means we deliver high-grade brass components on time and on budget.
Our approach is solution-focused: identify challenges early during prototyping, then apply proven fixes and scale up production confidently. (For example, we often supplement training with a short video demo of sand casting to highlight gating and pouring methods.) In the end, WJ Prototypes’ internal team and partners ensure that each brass casting – whether a single prototype or a multi-thousand-piece run – meets design intent and cost targets. This synergy of innovation, quality engineering, and scale is how we turn raw ideas into precision brass reality.
You can submit your designs to us through our contact us page
OR Email to info@wjprototypes.com